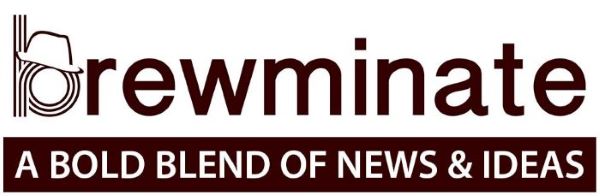
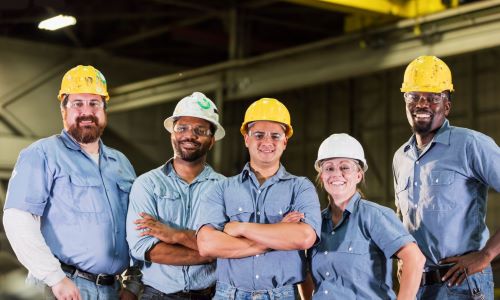
There are several known risks in manufacturing that can lead to serious injuries but if you take proper precautions, those risk can be significantly reduced. By the very fact that you are required to carry workers’ compensation insurance, you know that there is always a risk of injury on any job but within the manufacturing industry, injuries become much more common.
Anything from a broken part on a machine to wet floors that weren’t properly posted can cause a whole host of injuries you could be liable for. Bear in mind that your most valuable resource is the people you have doing their jobs day after day. It behooves you to take good care of them so they can, in turn, take good care of your company. Following are 10 ways to prevent injuries in manufacturing. Do you have all of them in place?
1. Provide PPE as Needed
This is something that came into the spotlight during the Covid-19 pandemic. However, Personal Protection Equipment (PPE) has always been around and has always been industry specific. In terms of manufacturing, this kind of protective gear could include earplugs to help prevent damage to the ears of workers subject to repeatedly loud noises. Also, those who are already wearing hearing aids should be given earmuffs instead or advised to turn off their hearing devices so they aren’t damaged as well. The PPE you use for your particular industry within the field of manufacturing will be specific to the work you do.
2. Invest in OSHA Certified Safety Training
Many of the jobs you do require OSHA certified safety training for any employees working on those tasks. Sometimes that certification is necessary before running heavy machinery and other times safety training can prevent falls such as when workers are doing their duties on high scaffolding. For example, that worker bolting on the exterior frame of a jumbo jet would be high above the ground, so safety training for working on scaffolding or when rappelling is mandated by the Occupational Safety and Health Administration, OSHA.
3. Carefully Assign Duties
It is imperative that you assign only qualified people to do the job. Taking the example of the jumbo jet mentioned above, if that person who is OSHA certified calls in sick and you don’t have anyone else to do his work, you’d need to either shut down production for that day or move people around so that only those trained in required safety procedures are on the job. You couldn’t very well bring in someone from maintenance, hoping to teach them how to use the power tools. There’s a much bigger issue at stake here. That person also needs to be certified to handle the dangers associated with the job. That’s written in stone.
4. Appoint a Safety Team Leader
Depending on the size of your manufacturing concern, you could either appoint a safety team leader from within or hire a safety inspector from the outside. It is extremely important that there is a person in charge of seeing to all necessary safety precautions for two main reasons. Primarily, you want to endure the safety of your workers and secondly, you don’t want to be found in non-compliance! That could be a costly mistake in terms of dollars and cents.
5. Conduct Regular Safety Inspections
The person you’ve designated as your safety team leader would be responsible for conducting regularly scheduled safety inspections. The best way to prevent accidents and health issues is to ensure that all precautions are in place and being observed.
6. Maintain Equipment Regularly
Just one broken or faulty bolt can be the cause of an entire machine suddenly coming apart. That could lead to serious injuries on more than one person, so it is imperative that you inspect, maintain and repair all equipment regularly.
7. Use the Right Tools
If one of your power tools suddenly breaks down, don’t try to substitute a sub-standard tool for the job. It is vital that every tool you use is rated for the jobs they are performing, so until you can get a replacement tool, call a halt to the job. A tool not designed for the job at hand could cause serious injury to the person operating it, so always keep that in mind.
8. Automation to Reduce Repetitive Strain
Some jobs such as those on a production line can be accomplished through repetitive actions. This can lead to muscle strain which, in turn, can lead to accidents. Such things as picking up the next heavy tray of parts that worker will be installing on a production line can cause tears in those muscles that have been strained through repetitive actions hour after hour, day after day. Some manufacturers are moving toward automation wherever possible to avoid a situation like this.
9. Schedule Breaks Wisely
Speaking of wear and tear on the body, for this reason many manufacturers schedule in an extra break so that their workers can stretch their muscles a bit. They can have that extra cup of coffee to keep them alert, which is also a great way to prevent serious injuries. Falling asleep on the job not only reduces production but it can also be extremely dangerous. Sometimes the mere act of getting up and moving around helps to get the blood flowing to the brain as well.
10. Ongoing Training
Finally, ongoing training is essential. Any time a new tool, piece of equipment or process is introduced, training should be offered at the same time. Not only does this enable workers to do their jobs well but it also helps to prevent mishaps due to working with unfamiliar tools or processes.
In any line of work, safety is important but in manufacturing with an alarming number of risks, it is all the more so. Always keep your staff well trained and your equipment in good repair. It is always better to prevent an accident than it is to deal with the consequences of one, so remember the old adage: an ounce of prevention is worth a pound of cure.