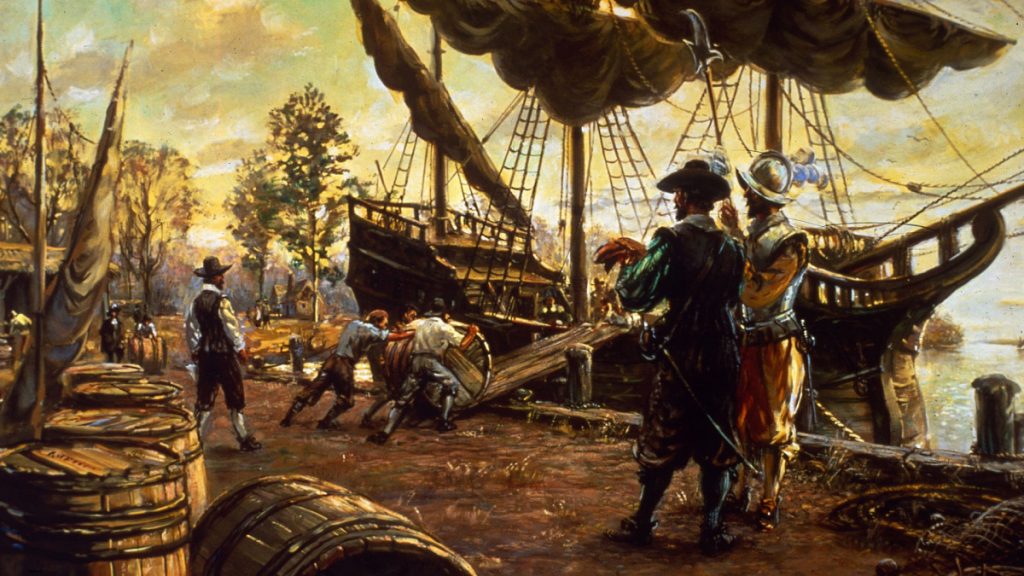
Brewing in the Seventeenth Century
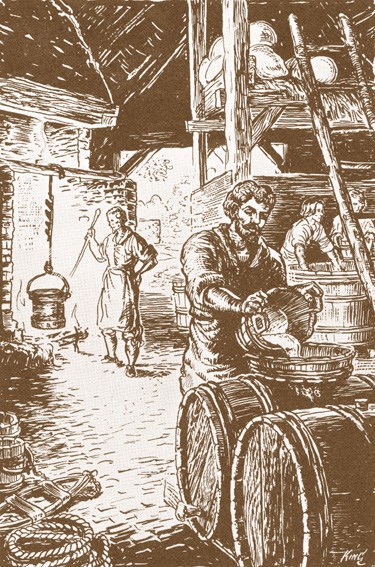
Oh we can make liquor to sweeten our lips
New England rhyme
Of pumpkins, of parsnips, of walnut-tree chips.
On May 24, 1607, the newly-arrived colonists at Jamestown had their first feast. George Percy reported that among the potables was beer, and, although the Virginia Company had expressed concern as early as 1606 concerning “that odious vice of drunkenes,” alcohol consumption was a way of life for the colonists long before they founded the first permanent English settlement in the New World. Beer, cider and other relatively weak fermented beverages were almost universally consumed from the earliest days of Virginia’s history. The colonists, in addition to importing the beer from the Mother Country, quickly began practicing the art of brewing themselves.
Beer, the result of the slow fermentation of malted and hopped liquid, is divided into three basic categories. Stout is a dark, heavy beverage with a relatively high alcoholic content. Lager, produced by a yeast which is activated at a relatively low temperature (40° F), is the lightest form of beer. In between these two extremes in both color and alcohol content is ale, which is produced by yeast which ferments best at about 60° F. Ale, because it was produced at a temperature which was more easily maintained, was the brew of choice in colonial times.
Producing a drinkable ale was not easy, and the colonists were not always successful, as the complaint from a 17th century inhabitant of Jamestown confirms: “I would you could hang that villain Duppe who by his stinking beer hath poisoned . . . the colony.” Unlike the sophisticated scientific methods employed in today’s breweries, the beer-maker of the 17th century relied on taste, smell and touch. In England, one of a housewife’s duties was the production of beer for her family and servants. Beer, from the Middle Ages well into the 17th century, was produced commercially by both men and women.
Many ingredients were added during the brewing process. The first step in making beer was choosing water of a pleasing taste. Fortunately for the consumer, all the boiling which took place in subsequent steps would destroy any dangerous bacteria. The grain, which gave the beverage its body (barley was the usual ingredient, although corn, oats, wheat and rye could also be used) had to be malted (sprouted then dried in kilns) before being added to the mixture. Sugar of some type, usually in the form of molasses or honey, provided nourishment to the yeast. Hops, the fruit of a vinelike plant related to the mulberry tree, gave the ale its characteristic scent and flavor.
To make beer, malt was soaked in a large wooden mash tub at low temperatures then separated out of the liquid and ordinarily used for animal food. The liquid, called “wort,” was transferred to the keeler, a large copper pot to which was added hops and other ingredients. After boiling the mixture for several hours, the brewer cooled it to about 70° F and sprinkled on the yeast, which began to digest the sugar in the solution and excrete it as alcohol. Bacteria and foreign yeast could spoil a brew, so it was important to keep the keeler covered. Stirring took place periodically, traditionally done with a bunch of broomstraw which was impregnated with yeast and quickened the action.
When fermentation was complete, the beverage would be either consumed right away or transferred to barrels for storage, leaving as much as the sediment behind in the keeler as possible.
Drug Production in the Seventeenth Century
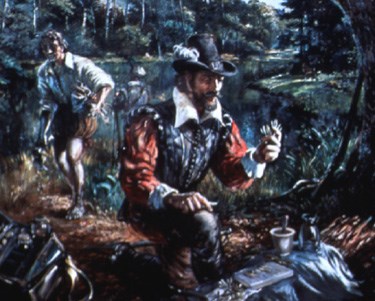
“If there were any conscience in men, it would make their harts to bleed to heare the pitifull murmurings and out-cries of our sick men. . . .”
George Percy, Observations
Although Jamestown was far from a lone island of sickness in the 17th century, the early settlers seemed to have more than their fair share of ill health. Poor diet, foul water and extremes of climate lowered their resistance; diseases ranging from smallpox to scurvy could carry them off easily.
The colonists were afflicted with bodily suffering, but they fought back as best they could. From the employment of tried-and-true remedies to the introduction of local substances into the traditional pharmacopeia, physicians and laymen worked to control an appalling mortality rate.
Most European medicine up until the Renaissance was based on Greek and Roman texts, particularly those of Hippocrates, Aristotle, Dioscorides and Galen. In addition to providing lists of plant materials and their medicinal uses, these sources taught that illness was the result of imbalance between the four humors of the body (black bile, yellow bile, phlegm and blood). They also stressed a reliance on theory rather that on direct observation.
Typically, a physician working in the Galenic tradition diagnosed a disease by determining which humor was out of alignment. He then treated the condition by either removing an excess of one substance or attempting to augment a weaker one. The former course was usually the approach of choice and attainable by either physical or chemical means. Venesection (bloodletting), sweating, blistering or clystering (administering enemas) were common physical means to balance a patient. By using powerful drugs, the sufferer could be induced to sweat, drool, urinate, defecate, cry or vomit to remove an imbalanced humor.
In addition to humoral theory, doctors could draw from a vast store of ancient herbal knowledge, derived through a combination of empiricism and application of sometimes bizarre theories. Dioscorides’ text describes over 500 plants and their uses.
After the fall of the Roman Empire, monasteries and local healers kept medicinal herbal lore alive in Western Europe. In the Mediterranean regions, however, Arabs dominated the culture in general and scientific thought in particular. When Crusaders from the West made contact with the Moslems, they “rediscovered” much lost learning, adding it to their more limited lore.
Among its many contributions, Arabic medicine gave Western Europe a new text to train physicians. Drawing heavily on the Greek and Roman sources mentioned above, ibn-Sina (Avicenna), a flamboyant and successful Arabian physician, stressed the reliance on theory over empirical observation. His Canon of Medicine was considered the highest medical authority until well into the 17th century.
Pharmacopeia was also altered by cultural contacts made during the Crusades. Heavily sweetened and spiced concoctions made from exotic materials became popular, and distillation was employed for the first time to extract alcohol and essential oils. Opium came into use in the west. At the same time, however, the old-fashioned herbal lore practiced by laypeople fell out of favor with the professional medical community, eventually coming to be seen as a threat to officially-sanctioned practice.
In the first half of the 16th century, there emerged from the alchemic tradition of Paracelsus an aversion to Aristotelian traditions and the recognition that doctors should rely more upon their personal observation of illness than on ancient texts and theories. Paracelsus, a controversial Swiss philosopher and scientist, also introduced the use of metals such as mercury and antimony in treatment of disease.
Physicians had never dismissed the healing properties of common plants out of hand. By the reign of Elizabeth I, the knowledge of herbs was considered an indispensable part of the training of housewives, stockmen and doctors alike. The age of the herbal had begun. These books, which described botanicals and their usages, were often beautifully illustrated and usually drawn largely from earlier sources. The best-known herbals are those of John Gerard (published in 1597) and Nicholas Culpepper (published in 1648).
New knowledge in medicine came with the discovery of new curative substances in the Western Hemisphere. Colonists brought the old, familiar plants with them from home, but they were also willing to experiment with the unknown. Common remedies discovered during this time included tobacco (good for everything from worms to lung congestion), Peruvian Bark (from which is derived quinine, the anti-malarial medicine), sassafras (at some times worth its weight in gold, since it was considered a sovereign cure for syphilis) jalap and ipecac (both powerful purgatives).
Physicians, whose training required many years of study and a large cash base, were few and, in any case, too expensive for the average person to afford. Instead, many people consulted apothecaries, who, until the reign of James I, had belonged to the Company of Grocers. James created the Apothecaries’ Society in 1617, and by 1634, over 150 apothecaries were licensed in London alone. In addition to supplying drugs, these men also diagnosed and prescribed for illnesses. Even the less costly apothecaries were beyond the means of the majority of the population, however, which relied on a local herb woman or cunning man instead, with the occasional trip to the barber or surgeon for bloodletting or toothdrawing.
Production of plant-derived cures, whether by a physician, an apothecary or a layperson, could be a complex process. Some medicinal substances were imported from other countries. Others had to be gathered, either from the wild or the garden. Most colonists with a kitchen garden grew medicinal herbs such as hyssop, lavender, comfrey and fennel interspersed with the vegetables and flowers.
Timing was important in gathering botanicals because weather, temperature, the time of day and the phase of the moon all were assumed to affect the potency of the drugs produced. Seeds, stems, leaves, bark, flowers and roots could all be used, depending on the plant and treatment. Most botanicals were air-dried, hung upside down in a hot, dry place or cut into pieces and dried on screens.
After the herbs were completely dried, they could be transferred to opaque containers for longer storage. Whenever possible, the plant material was left intact until actually needed for treatment; grinding or powdering tended to decrease its usefulness by dissipating essential oils.
Some medicines consisted of only one botanical, and were referred to as “simples.” Compounds were combinations of inactive and at least two active ingredients.
Preparation methods varied as well. Infusions were boiled for ten minutes over the fire to produce a stronger medicine. Decoctions were produced when boiling might destroy potency, combining the drug with hot water and leaving the mixture to steep for hours or sometimes days.
In some cases, the oils, resins or waxes of the plant were not water soluble and had to be dissolved in alcohol, resulting in a tincture. Syrups were produced when the plant material was added to water, boiled down and combined with a sweetener like honey which also acted as a preservative. Essential oils could be extracted from botanicals by steam distillation or by soaking large quantities of the plant in small amounts of oil for a long time. Pills were produced with the combination of active ingredients with a filler such as wax, bread dough or gum arabic.
Treatments could also be external. Creams and ointments were herbal oils combined with beeswax or fat to produce a compound which was solid at room temperature. Compresses, poultices and plasters were plant materials applied externally, usually in combination with heat or moisture.
Botanical remedies remained important medicinally. By the middle of the 19th century, organic chemists were beginning to isolate specific active ingredients in medicinal plants, but 80% of pharmaceuticals were still derived from botanical sources by 1900. This would soon change. Due to cost of production and storage, as well as the varied concentration of an active ingredient from locale to locale and even from plant to plant, drug companies concentrated on replicating cheaper synthetic versions of active ingredients. Although chemists have been largely successful, at least 25% of prescriptions filled by pharmacists today contain active ingredients from plants.
Glassmaking at Jamestown
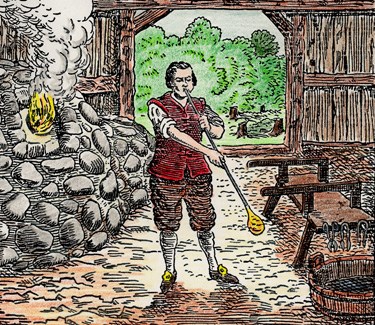
Glassmaking in America began at Jamestown, Virginia in 1608, where a glass factory was operating just a little more than a year after the first colonists arrived from England. The “tryal of glasse” sent back to England that year was not only the first glass made by Englishmen in the New World, but was also their first factory-made product.
Businessmen in England made up the London Company. With a new continent to draw upon, they hoped to find valuable raw materials needed back home. They also hoped to manufacture goods that could be sold for a profit. One of the possible industries for which Virginia seemed suitable was glassmaking. In the past 50 years, there had been a great increase in the demand for glass, but this demand could not be satisfied by the English factories. Few Englishmen were skilled in the craft, and though foreign glassmakers had come from the continent to practice their trade and had presumably trained some Englishmen, a great deal of glass was still being imported. Expansion of the industry had been limited by the gradual depletion of the forests, for coal was just beginning to be used in furnaces.
Captain Newport had explored the vicinity of Jamestown and would have known that the resources needed for glassmaking were readily available in the new land. The officials of the London Company had every reason to believe glassmaking in Virginia was entirely feasible and a likely source of profit. It seemed reasonable to assume that the cost of glass from a factory in Virginia would be much less than what was being paid in Italy and other continental glass centers.
But enlisting English glassmakers to leave a flourishing industry at home and set up business in a strange land across the ocean was not easy. Therefore, the Company looked abroad, and among the 70 settlers who sailed for Virginia in the summer of 1608 were “eight Dutchmen and Poles,” some of whom were glassmakers. The so-called Dutchmen probably came from Germany, for Captain John Smith in one of his letters mentions that the London Company had sent to Germany and Poland for “glasse-men and the rest,” “the rest” referring to the makers of pitch, tar, soap ashes and clapboard. It was also customary to refer to Germans as “Dutchmen.”
The introduction of glassmaking in the fall of 1608 appeared at the time to increase the chances for the colony’s success. The glass factory, according to Smith was located “in the woods neare a myle from James Towne” or, as William Strachey described it, “a little without the Island where Jamestown stands.” There, as Strachey wrote, the glass workers and their helpers erected a glasshouse, which was “a goodly howse…with all offices and furnaces thereto belonging.”
When Captain Newport left for England later that year, he carried with him “tryals of Pitch, Tarre, Glasse, Frankincense, Sope Ashes; with that Clapboard and Waynscot that could be provided.” Of what this first “tryal of glasse” consisted, the records do not tell.
The records do indicate that there was some activity at the glass factory during the first six months or so following its establishment.
Twelve years later a second glassmaking venture was started at Jamestown. Well planned, reasonably well financed, and staffed with experienced Italian glass workers, it appeared to have a much better chance of success than the earlier venture.
This second venture was organized largely through the initiative of Captain William Norton. In June 1621, he petitioned the London Company for a patent to “sett upp a Glasse furnace and make all manner of Beads & Glasse.”He proposed to take four “Itallyans” and two servants to Virginia, who were to have the glasshouse operating within three months after their arrival. They sailed for Jamestown in August 1621.
The Italians proved difficult for the English to work with, and there were other difficulties. First the glasshouse blew down and then the Indian uprising of 1622 put a stop to everything for the time being. Finally, Captain Norton died, and the Italians “fell extremely sick.” George Sandys, resident treasurer for the Company, took over the project upon Norton’s death, but fared little better in getting results. He repaired the furnace and the crew set to work in earnest in the spring of 1623, but without success.
In a desperate effort to make something of the enterprise, Sandys even sent to England for sand that might better suit the glass workers, but he finally was forced to give up completely in the spring of 1624. The records suggest that little, if any, glass was made during this second and last glassmaking venture at Jamestown.
Archaeological excavations did not disclose what kinds of glass were made at Jamestown during the two ventures. When the glasshouse site was excavated in 1948 only small, dark green fragments and drippings were found. Experts who studied the fragments believe that they could have been pieces from window panes, small bottles and vials, and simple drinking glasses.
At Glasshouse Point, located one mile from the visitor center, the National Park Service exhibits the original furnace ruins. Nearby is a reconstructed glasshouse, built in the 17th century style. At the Glasshouse, costumed artisans blow and fashion glass in the 17th century manner. The handmade objects are sold at the Glasshouse.
Flax Production in the Seventeenth Century
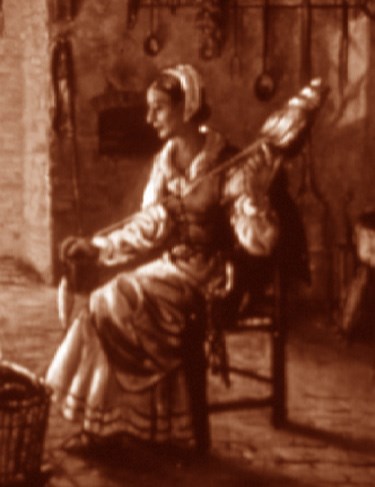
When Sir George Yeardley returned to Jamestown in 1619, one of his instructions from the Virginia company of London was to promote flax harvesting. The stockholders hoped that, as with silkworm cultivation, viticulture and glass production, the colonists would use this ancient crop to both realize a profit and diversify their labors.
Ultimately, none of these ventures was a commercial success. The labor involved was either too intensive or required too much skill, the climate and soil of the Chesapeake region did not cooperate, or plain bad luck attended the operations. That did not mean, however, that wine, silk or linen were never produced in Virginia. Although flax, the plant from which linen is derived, never rivaled tobacco as a cash crop in the Chesapeake, most farmers and plantation owners grew small amounts will into the 1800’s for their own use.
The plant which provides the raw material from which linen is made is an annual which grows two to three feet high on a slim, little-branching stem. It is this woody stalk, hollow when dried, which is harvested and ultimately manufactured into linen.
Spinning flax into thread is facilitated by properties inherent to the fiber, including its length (two to three feet when will prepared), its high pectin content (when wet, the pectin acts as a glue to further bind fibers together) and the nodes which appear along the length of the fibers (similar to those found on bamboo) which incline them to join even more readily.
Additional properties of flax make it a desirable finished product. Other than ramie, it has the greatest tensile strength of any natural fiber, and is 20% stronger when wet. It is highly absorbent and dries quickly, and its high wax content gives it linen’s characteristic luster. It is also long lasting. If not exposed to synthetic bleaches or mechanical drying, a regularly-used linen sheet can survive for a century or more. Making flax an even more valuable crop, the seeds can be harvested and linseed oil (used in wood treatments, paint and animal fodder) extracted.
Flax has been with humankind long before Europeans’ discovery of the Western Hemisphere. Linum angostifolium, the wild ancestor of flax, can be found from the Black Sea to the Canary Islands. L. usitatissimum (meaning “of greatest use”), is the oldest cultivated fiber plant, with evidence of its growth and use dating back to the fifth millennium BC in both Mesopotamia and Egypt. While the former concentrated on wool production, the latter, employing the fertile fields of the Nile Delta, became experts at the creation of linen textiles which cannot be rivaled in strength and fineness of weave today.
Egyptians turned the coarser, low-grade flax into rope and string; the finest quality was reserved for clothmaking. Workmen’s wives set up makeshift looms in the doorways of their dwellings to weave linen for household use. Female serfs and slaves worked endlessly in crews on large estates; in unplundered tombs hundreds of sheets are commonly found, stored up in anticipation of the departed’s return. Linen fabric, millennia before coinage was invented, served as a medium of exchange and a measure of wealth.
L. angustifolium grows wild in Briton and was employed as early as 3000 BC by the Swiss Lake dwellers. Because these people centered their communities over swampy areas, many wooden and fiber artifacts have survived from their culture. Tools for flax preparation, hanks of spun thread and cloth of complex weave have all been found in the alkaline lake mud.
L. usitatissimum is believed by many historians to have been introduced into England by the Romans; by the 16th century, laws were enacted requiring that a quarter of an acre (one rood) of flax be planted for every sixty acres under cultivation. Linen and wool were the two most common fibers, often combined in linsey-woolsey, a fabric with warp threads of linen for strength and weft threads of wool providing bulk and warmth.
Although flax has many advantages as a fiber crop, its overwhelming disadvantage is the amount of labor, skilled and otherwise, required from sowing to harvest.
Flax needs a deep, rich soil, and, like tobacco, quickly depletes the nutrients from the land where it is planted. In early settlement days in Virginia, that meant it could only be raised on newly-cleared ground. After two or three years of a flax crop, a farmer needed to sow a less nutritionally-demanding crop, such as wheat. Later in the colonial period, farmers could incorporate flax into a rotation process which included heavy dunging or the sowing of cow peas a year or two before the next flax crop was to be planted.
After plowing in November, February and March, the ground was harrowed and raked fine. The small, oily flaxseeds were sown broadcast in April and a final harrowing took place. The closer the seeds were spaced, the less branching took place in the resultant plants and the higher the quality of the crop. If flax is sown properly, weeding is unnecessary because there is no space for unwanted plants.
Flax takes about a hundred days to mature. When the leaves yellow and the seed turn brown, the flax is pulled from the ground by the roots, spread to dry for a few days, and, if time was not a factor, stored until the next year to age.
Processing flax is an extremely labor-intensive process, providing skilled and unskilled employment for both adults and children. First, the upper part of the flax bundles are drawn through coarse combs to remove seed in a process called rippling.
After the seeds are removed, it is necessary to separate the long, silky inner fibers which constitute the end product from the straw and inner pitch. Retting, in which the unwanted fibers are loosened and decomposed, can be achieved in several ways. The flax can be left out in the field, where the exposure to the elements, particularly the moisture in the air, can do the work. A pond or through can be used to achieve the same effect in much less time, but with a prodigious odor. The ideal way to ret flax is to expose it to constantly running water, such as a stream. The amount to time this step requires depends on the quality of the flax, the temperature and numerous other variables.
When the straw comes away easily from the few bent fibers, it is time to grass the flax. The bundles are untied and laid in a field for a few days until they are dried on one side, then turned so the other side can be dried. When the crop is thoroughly moisture free, it is stacked inside to age for a few more weeks.
Next, a series of steps free the linen fiber from the boon (unwanted plant material). The brake, a large wooden machine, is used to break down the trash material and loosen it further from the end product. Then the flax is scutched (beaten against a board with a blunt wooden knife). The final process is hackling, in which the fiber is drawn through a series of metal combs to remove the last of the boon and shorter fibers. The end result is a strick, a half-pound bundle of long, light grey fibers which resemble human hair. Over 85% of the plant has been removed before the strick is produced. Some of the shorter fibers removed during hackling can be used as tow for sacking or inferior cloth.
Since flax is such a long fiber, special care must be given before spinning to keep it from tangling. A distaff is a tool which keeps the fibers separated and properly aligned during spinning. Thread is produced using the small wheel often called a flax wheel. An experienced spinner has little difficulty creating a fine, strong thread with flax. In order to produce a smooth yarn, however, she must also be able to moisten the flax continuously as she is spinning.
After the thread is spun, it must be stretched and boiled to set the twist put into it by spinning. Bleaching can be done either before or after weaving, by exposing the fiber to sunlight for prolonged periods or using such chemical treatments as chloride of lime, soap and soda or lye water.
Today, Eastern Europe produces 80% of the world’s flax crop. France, China, Egypt, Holland and Belgium provide flax as well. Due to increasingly efficient mechanical harvest and processing, this ancient fiber is becoming more popular than a generation ago.
Silk Production in the Seventeenth Century
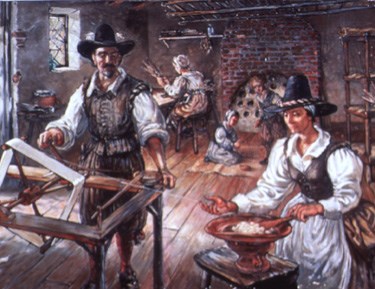
“Silke is a marvellous hopefull commodity in this Country.”
John Pory to Sir Edwin Sandys, June 1620
For thousands of years, silk has been considered a luxury trade good par excellence because it fetches a high price, is relatively easy to transport and is always in demand among the wealthy. It is only natural that James I and subsequent English sovereigns would encourage production of this textile amongst the settlers of Virginia.
Chinese legend tells how silk was discovered almost 5,000 years ago by Xiling Shi, the wife of the semi-mythical emperor Huanghi. Walking in the garden, the empress plucked a cocoon from a mulberry tree. The cocoon fell by accident into her cup of tea and she watched as a strong white thread unraveled. However it was discovered, the potential for such a thread was first realized in China, where silk fabric was being produced by 3000 B.C. A silk industry had developed there by the 14thcentury B.C.
The Silk Road, a trade route which involved many cultures and stretched from Nagasaki, Japan in the east to Genoa, Italy in the west, opened by 100 B.C. As its name implies, the major product being traded from east to west was silk, the manufacture of which the Chinese kept a closely-guarded secret. Other peoples in central and western Asia learned how to spin and weave the threads, but only the Chinese could supply the raw materials.
This situation altered in the fifth century A.D., when a Chinese princess married the king of Khotan, an oasis north of the Plain of Tibet. When the princess left her native land and traveled west to her bridegroom, she carried, smuggled in her headdress, silkworm cocoons and the seeds of the mulberry tree on which they feed.
Silk spread even further west by similar ploys. In 552 A.D., Persian Christians visiting Khotan hid silkworm cocoons in their hollow walking sticks, subsequently delivering the means of silk cultivation to Justinian I of Byzantium. Though this story is the stuff of legends the fact remains that silk production began in the Byzantine Empire at that time. From the sixth to the thirteenth century, the silk brocades of Constantinople were highly sought.
Sericulture (the craft of producing silk and its cloth), gradually spread through western Asia and Europe. By the 15th century, France and Italy were the leading manufacturers of silk in Europe. Due to religious persecution, large groups of skilled Flemish and French weavers fled to England, and an industrial complex for silk weaving developed at Spitalfields in the 1620’s.
Silk has many properties which contribute to its reputation as a luxury fiber. It has a beautiful natural luster and will take dye readily. Almost as strong as cotton, it is more elastic than either cotton or linen. It will absorb up to one third of its own weight in water without feeling wet to the touch, and is a warm fabric despite its lightness. Silk has some negative attributes as well. It is easily harmed by sunlight and certain chemicals, including the salts in human perspiration. It is a poor conductor of electricity, which contributes to its reputation for “static cling” in dry atmospheric conditions.
Producing silk is a complex and skilled operation which has taken centuries to refine. The silkworm moth (Bombyx mori) has been domesticated for centuries, and the result is a creature which is bred and raised on farms, with wings too weak to fly and legs unable to crawl more than a foot or so. Silkworms are totally reliant on humans and thus a very labor-intensive prospect.
Although most silkworms raised for the industry are killed before they undergo metamorphosis and emerge as adults, the powdery white moths which do emerge from their cocoons have one primary function in the few weeks they remain alive: to produce the next generation of silkworms. In the wild, pheromones secreted by the female help guide the male to her; in captivity, the same odors exert the same fascination. After mating, the female lays 500 yellow eggs, each the size of the head of a pin, which are attached to any surface by the sticky substance accompanying them. Eggs can be stored in cool conditions by farmers until it is time to hatch them, then transferred to incubators.
The larvae which emerge from the eggs about 20 days later are an eighth of an inch long. Feeding is the primary activity of the larval stage, which lasts about 25 days. During this period, the worm molts four times, becoming much larger each time it sheds its skin. At the last instar (the period before or after molting), the larva will have grown to 10,000 times its hatching weight. The worm eats almost continuously, fed on the leaves of mulberry trees brought to them by the farmers. As the worm grows, its special silk glands grow as well, eventually comprising one quarter of the larva’s mass.
At the end of the fifth instar, the worm stops eating. That is the signal for the farmers to transfer larvae to specially-constructed frames which will provide support for the worm’s construction of its protective and valuable cocoon.
By this time, the worm’s two silk glands are fully developed, and it begins to exude silk from both at the same time, as well as a sticky substance called sericin to bind the two threads together. The silk is liquid in the worm’s body, but hardens into a thread in contact with the air as the larva moves its head in a characteristic figure eight pattern.
After constructing a support system composed of short threads, the worm begins spinning its cocoon of a single, continuous thread of silk over a mile long. Constructed from the outside in, the cocoon takes over two days to complete. The worm then enters its pupae stage, which, if allowed to continue, will result in an adult moth in about three weeks. Most of the insects, however, are killed in the pupae stage, as they damage the cocoon when they emerge as adults. Roasting the cocoons in a hot oven is a malodorous process which kills the animals without damaging the silk they have spun.
To transform cocoons into cloth, workers boil them to release the sticky sericin on the outside. Next, since an individual silk thread is too fine to handle, the threads of as many as ten cocoons are wound together onto a reel, sticking together to form one long, strong thread. From then on, the silk can be treated as any ordinary fiber, either woven or knitted with the possibility of a wide range of textures and quality.
Although Stuart monarchs encouraged the production of silk in Virginia, the specialized labor force required, limited diet of the silkworm (the larvae did not relish the native mulberry trees) and the development of tobacco as a more successful cash crop ensured sericulture’s failure in the colony. Today, most silk is produced in China, Japan or Korea, with small quantities harvested in Russia and other countries.
Bibliography
- Barber, Elizabeth Wayland. Women’s Work.
- Beverley, Robert. The History and Present State of Virginia.
- Bonnett, Kendra. A Report on Drinking and Beer Brewing in the Seventeenth Century.
- Clark, Alice. Working Life of Women in the Seventeenth Century.
- Clendening, Logan. Behind the Doctor.
- Darlington, William. American Weeds and Useful Plants.
- Davenport, Elsie G. Your Handspinning.
- Diderot, Denis. A Diderot Pictorial Encyclopedia of Trades and Industry.
- Fannin, Allen. Handspinning: Arts and Techniques.
- Goodrich, Frances Louisa. Mountain Homespun.
- Gordon, Lesley. Green Magic.
- Harrington, J. C. Glassmaking at Jamestown. Richmond: Dietz Press, 1952.
- Hartley, Dorothy. Lost Country Life.
- Hughes, Thomas P. Medicine in Virginia 1607-1699.
- Johnson, Sylvia A. Silkworms.
- Kluger, Marilyn. Your Handspinning.
- Kowalchik, Claire and Hylton, William, editors. Rodale’s Illustrated Encyclopedia of Herbs.
- Linder, Olive and Harry. Handspinning Flax.
- Leach, Charles. Colonial American Fiber Crops.
- Meyer, Virginia M. and Dorman, John Frederick. Adventures of Purse and Person.
- Miller, Johnathan. The Body in Question.
- Neil, Edward D. History of the Virginia company of London.
- Notestein, Wallace. The English People on the Eve of Colonization 1603-1630.
- Reid, Struan. The Silk and Spice Routes: Inventions and Trade.
- Ross, Mabel. The encyclopedia of Handspinning.
- Rouse, Parke. Planters and Pioneers.
- Smith, Captain John. Adventures and Discourses. Detroit: Singing Tree Press, 1969.
- Thomas, Keith. Religion and the Decline of Magic.
- Wilbur, C. Keith. Revolutionary Medicine.
- Williams, Guy. The Age of Agony.
Originally published by the National Park Service, 02.26.2015, to the public domain.