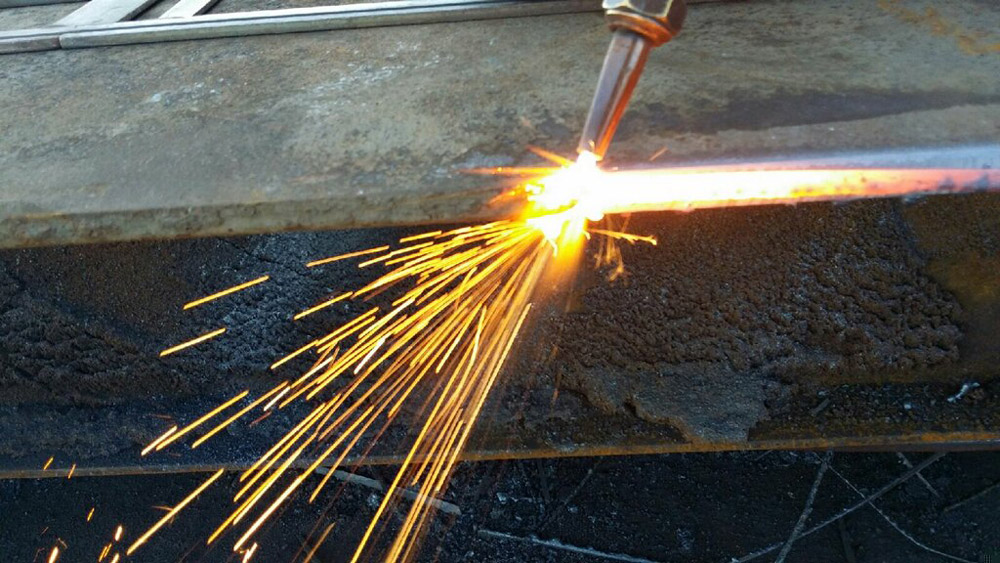
Let’s make us familiar with an industrial process of cutting different metals – Oxyfuel Cutting. This thermal process is considered highly economical across the globe for several reasons. One can understand it by delving into the entire procedure and getting known of everything related to oxyfuel flame cutting.
The process takes the help of oxygen and varied fuel gases like propane, acetylene, propylene, natural gas & MAPP to cut through assorted materials with absolute perfection. Since one can cut versatile thicknesses ranging from 0.5 mm to 250 mm through this process and find the cost of equipment within reach, oxyfuel cutting is widely used to overpower other alternative ways.
The Basics of the Process
If you take interest in knowing the entire cutting process in detail, you’ll have to go through a perfect demonstration of how it works. It is actually a combustion process that uses the flame produced by oxygen and fuel gas. The heating flame generated by a blend of oxygen and the fuel gas brings the specific metal up to its ignition temperature, but below enough the melting point of that material.
A jet or spurt of 99.5% pure oxygen is then blown on the preheated area of the metal. As a result, an exothermic chemical reaction takes place between oxygen and that metal since the oxygen jet oxidizes it to produce slag and a fine cutting kerf is formed. The slag is then removed away from that kerf to facilitate the jet to perforate through the metal and keep the cutting process continued.
With the help of high end, industry-grade oxyfuel cutting machines, the process can be implemented in an economical & hassle-free way. Based on the surface condition of the metal, its thickness and cut-velocity, the quality of that material’s cutting can be evaluated to help you take further steps. Several alloys steel that have the material thickness up to any number of inches can be finely cut with this industrial process.
Although some of the advanced cutting processes such as Laser and Plasma cutting have an increasing popularity today, oxyfuel cutting is still being a worthwhile & cost-effective choice to meet several industrial purposes. There can literally be no better substitute to surpass this process for higher material thickness up to 35 inches or so.
Major Points to Remember for Accurate Oxyfuel Cutting
There are some fundamental requirements without which oxyfuel cutting can be a mishap:
- The metal’s ignition temperature should be much below its melting point or else the metal would dissolve quickly and flow away right before the process of cutting.
- The melting point of the oxide should be much less than that of the neighboring material so that the oxygen jet can mechanically blow away that oxide or slag as well.
- A sufficient oxidation reaction between the metal & oxygen is needed to retain the ignition temperature of that metal.
- The gaseous reaction products in the least quantity must be needed for not diluting the cutting oxygen.
- Since some of the metals like stainless steel, cast iron, and other non-ferrous metals produce refractory oxides whose melting point is higher than that of their metals, the powder must be added to the flame in order to generate a fluid slag of lower melting point.
Salient Features of Oxyfuel Cutting
Every mechanical process does own a number of distinct features and oxyfuel cutting is no exception to that rule. The process assures multiple benefits and some of its key features include:
- Lower speed of cutting
- Impressive cut quality
- Smooth surfaces of cut
- heat input is good
- suitable for an extensive range of metal
- Carbonizing as well as hardening in the heat affected area
- Metallurgical great or oxidized surfaces
Usage & Transparency of Oxygen
As mentioned earlier in the above section describing the fundamentals of this process, the oxygen used in oxyfuel cutting method must be 99.5% pure. It is the purity of the oxygen jet that determines the cut quality and cutting speed of the process. That is why nozzle design remains highly accountable for shielding the oxygen jet from air entrainment.
The purity of oxygen must be 99.5% as a minimum. A decline of 1% in purity will naturally lessen the cutting speed by almost 25% and amplify the consumption of gas by 25%. It is typically evident from the name of the process that oxygen plays a substantial role in cutting a material.
Uses of Fuel Gases
When it comes to considering the quality & speed of cutting, there are multiple fuel gas variants as well as nozzle design choices for adding to the overall performance. The combustion of fuel gas takes place in two separate zones. In the primary flame, the fuel gas mixes with oxygen to produce carbon monoxide & hydrogen for acetylene. In the secondary zone of the flame, the combustion is carried on by supplying sufficient oxygen from the air.
The fuel gases required to implement the process are typically described by three particulars things – the amount of fuel gas to oxygen ratio, flame temperature and heat of combustion. Some of the widely used fuel gases include acetylene, propylene, MAPP (methylacetylene-propadiene), propane and natural gas.
There are specific properties of each gas to know before you choose them to use in the process. The heat distribution and flame temperature within the outer & inner flame cones can evaluate the comparative performance of the used fuel gases based on cutting speed, exact pierce time and cut quality. Besides oxygen, the role of fuel gases is equally important to execute the operation.
Conclusion
This flame cutting process guarantees perfect hole-piercing as well as high-quality cut to fulfill the exact needs. Through the process of oxyfuel cutting, you can easily obtain the specific material to its finished size of your choice without any necessity of additional processing. The process ensures seamless Y, K & V cut to be created by oxyfuel cutting machines. That is why several industrial hubs across the world rely on the accuracy and low-cost facility of this cuttin technique to a great extent.