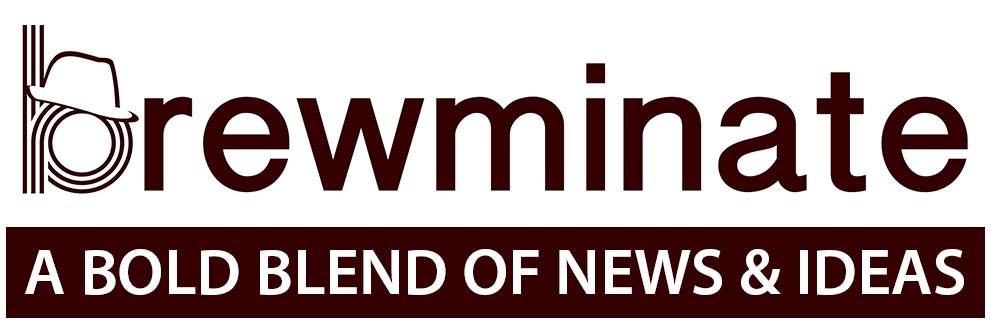
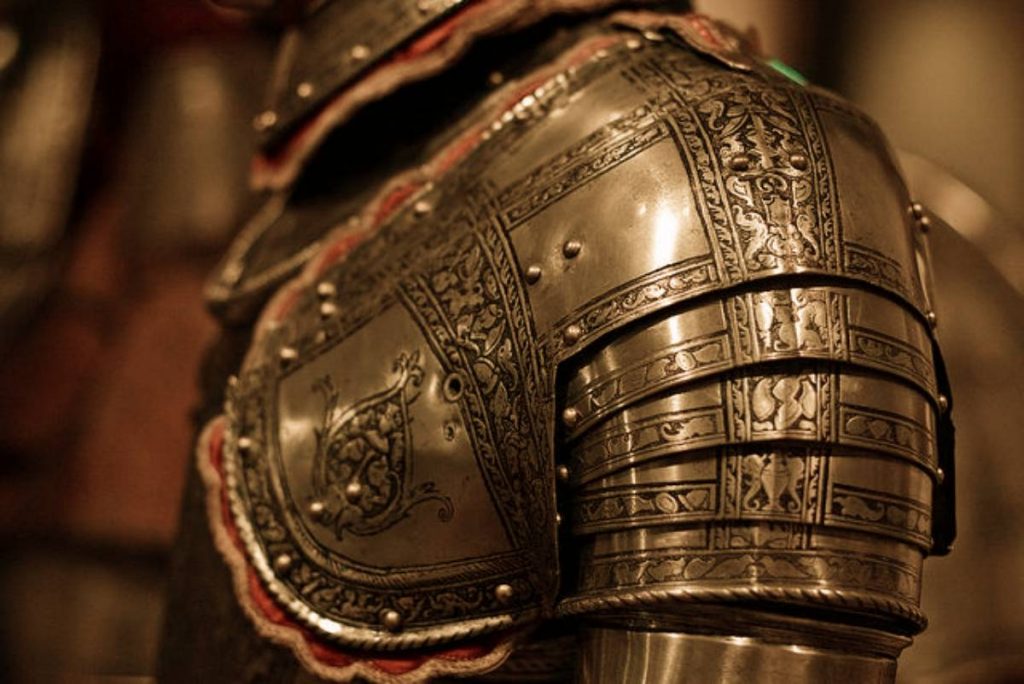
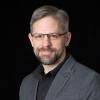
By Edward Hunter
Armorer and Conservator
Metropolitan Museum of Art
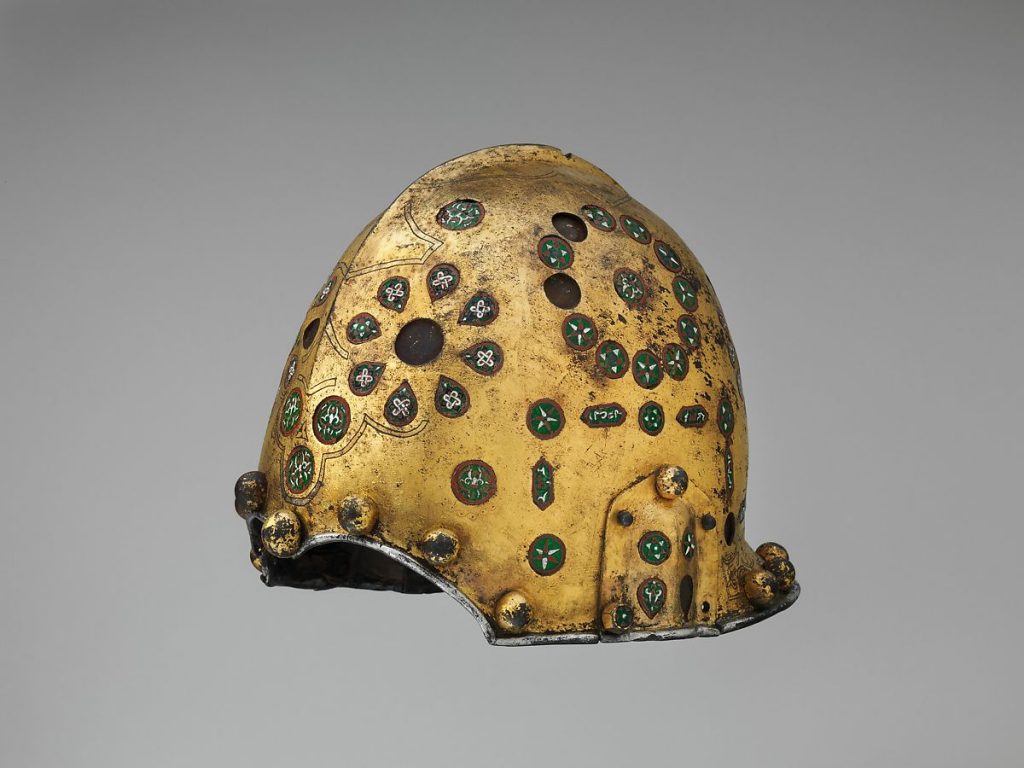
Gilding is the application of gold to the surface of some other material. Many techniques exist for doing this. A surface may be inlaid with gold wire (often referred to as damascening), or overlaid with thin sheets of gold attached mechanically, usually by burnishing gold foil onto a hatched surface. A very common way of gilding is to adhere gold leaf to a surface with an oil-based adhesive or a water-soluble size over gesso, as is typically used on picture frames , for example. A far more durable and long-lasting process is amalgam gilding, more commonly called “firegilding” or sometimes “mercurygilding.” This method is especially well suited to metalwork applications, particularly iron and steel—as seen in arms and armor —and bronze, used in sculpture and furniture mounts (“ormolu”).
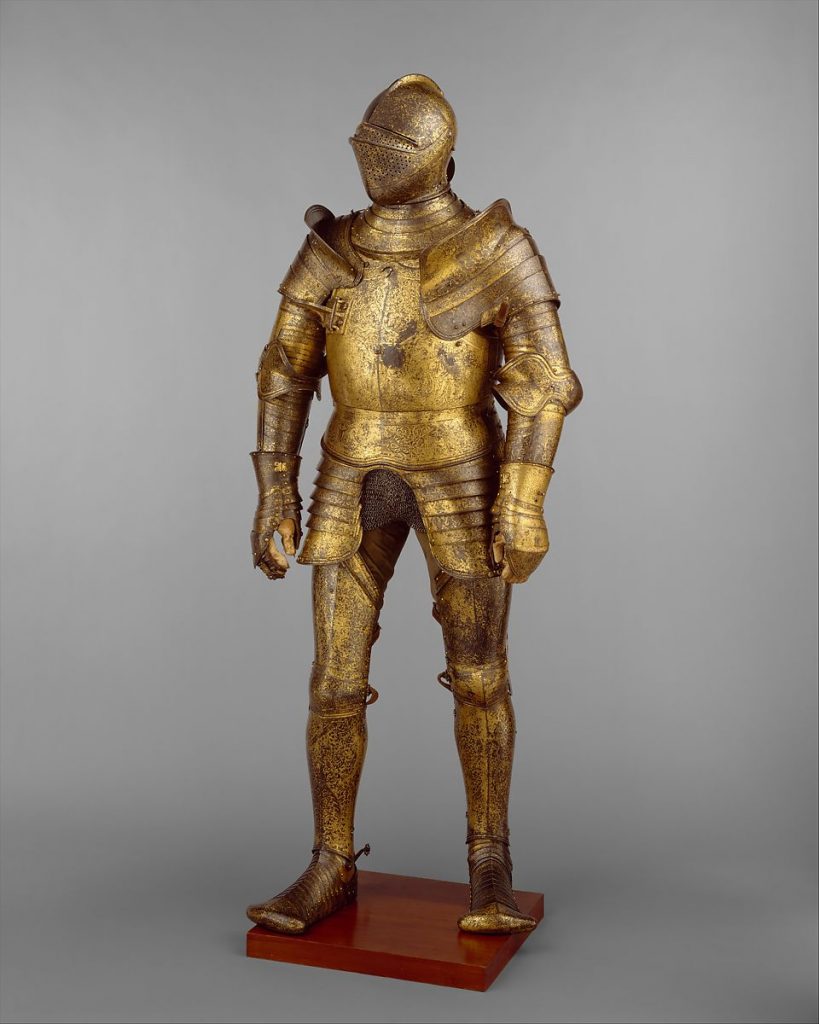
The Arms and Armor Department of the Metropolitan Museum has many splendid examples of fire-gilt armor and weapons on display. Perhaps the most striking example is the armor for field and tournament, which has been gilt in its entirety, primarily for its stunning visual effect, but also to protect the delicately etched steel surface from corrosion.
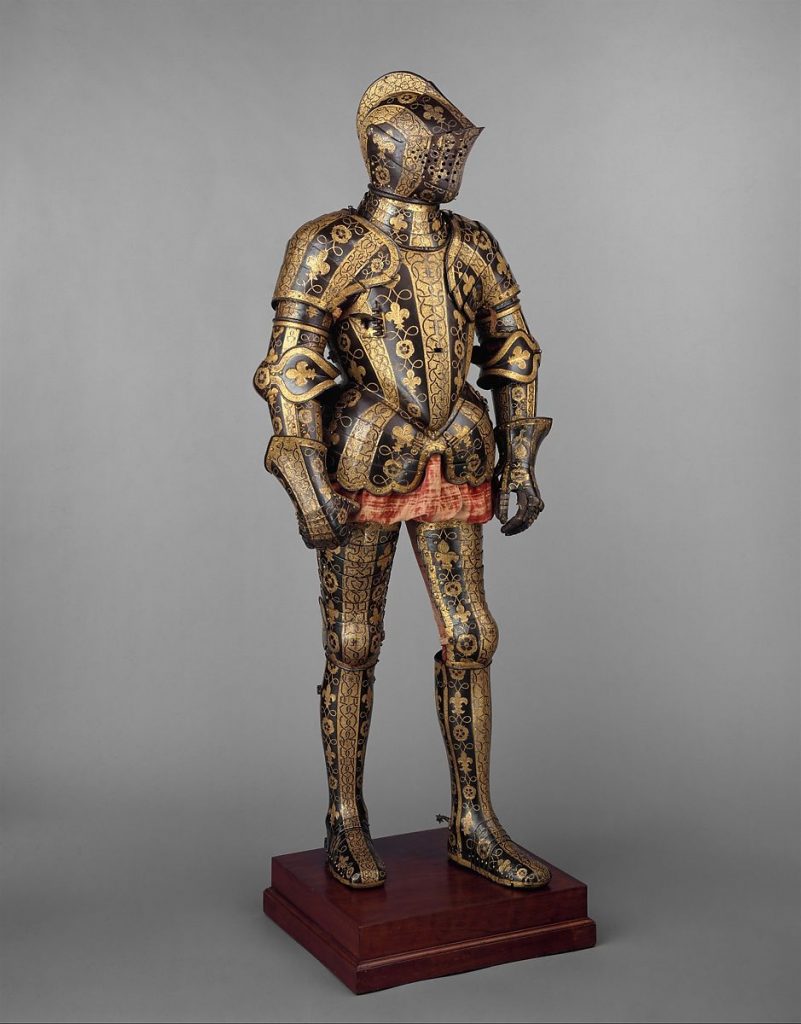
Equally impressive is the combination of bluing and gilding shown in the armor of George Clifford, with its distinctive contrasting patterns of gold and heat-blued steel. Firegilding could also be easily applied in the recesses of etching, on rivet heads, or as part of an area of decoration.
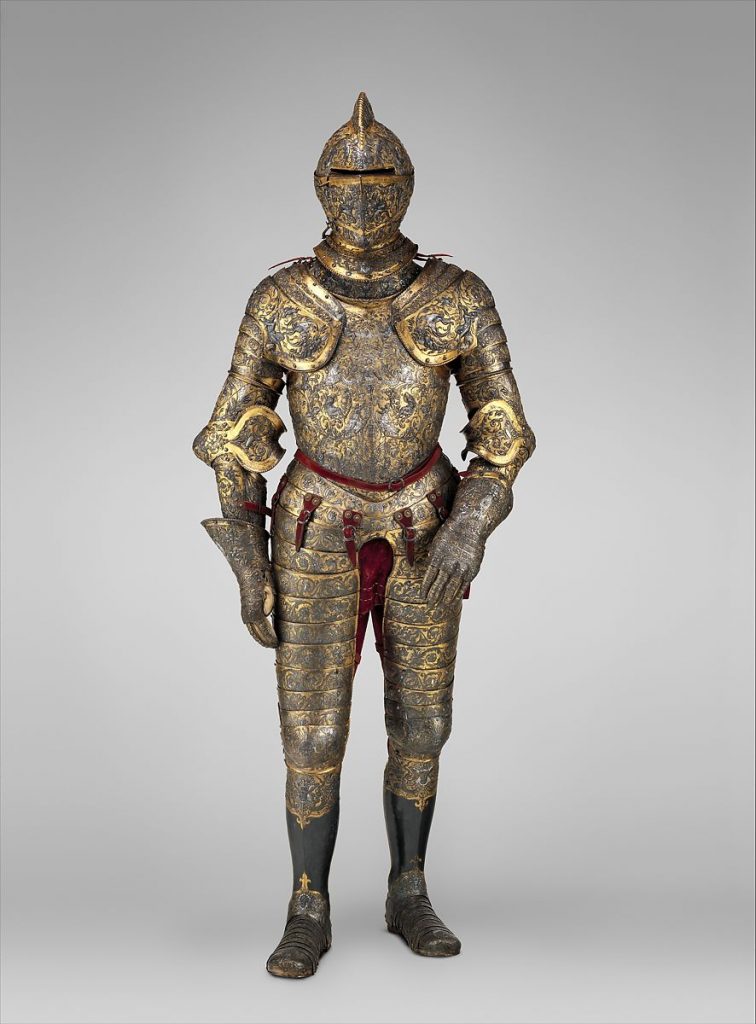
The armor for Henry II of France combines gilding with an elaborately embossed surface, areas of bluing, and areas of silvering, creating a sumptuous and lavish appearance.
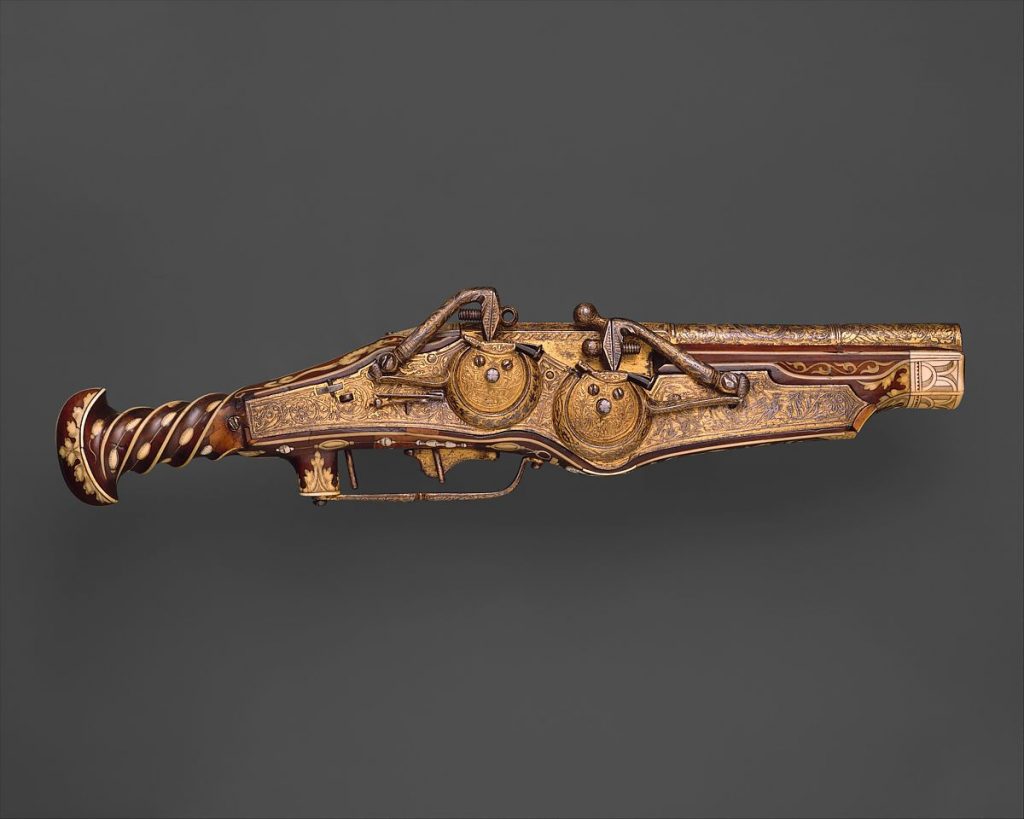
Weapons were also routinely decorated using firegilding. For wealthy clients, such as the emperor Charles V , the barrel, lock, and mounts could be gilt with splendid results, whereas it was regular practice even on otherwise austere pieces to gild the interior of the priming pan to prevent corrosion.
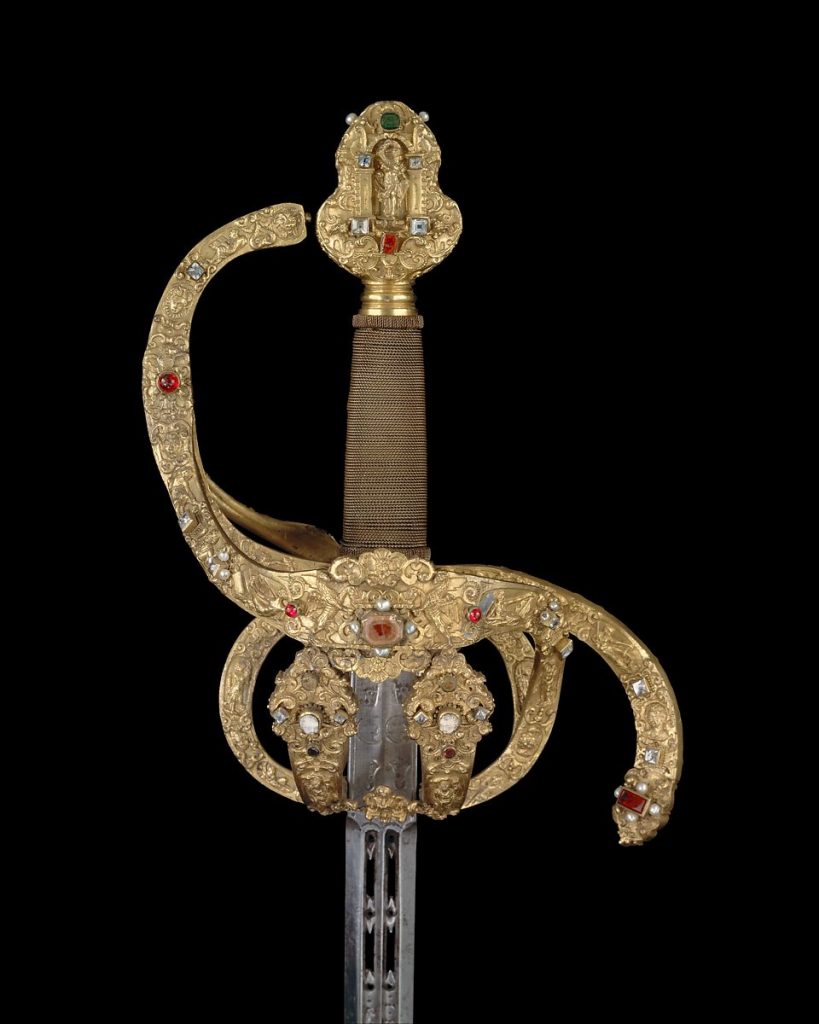
Swords and other edged weapons could be fire-gilt as well—usually on the hilt, but also along the blade and on various parts of the scabbard furniture. The decoration of arms and armor with gold was so popular that in 1618, when James II of England issued an edict restricting the use of gold in ornamental display (fearing its effect upon the national treasury and gold reserves), he prudently included an exemption for its use with armor and weapons (Ffoulkes 1912, p. 18).
The practice of amalgam gilding goes back many centuries. It was used by the Romans to apply gold onto silver, known as silver-gilt (Maryon 1971, p. 262), and in his twelfth-century book, On Divers Arts, Theophilus describes in detail how to gild a surface using an amalgam. An amalgam is any alloy of mercury with another metal, in this case gold.
The amalgam itself is prepared in various ways, but essentially involves mixing small pieces of gold and mercury. A mixture of one part gold to eight parts mercury is ground together in a mortar and pestle in a process called milling. This results in a paste that must be slowly heated and stirred with an iron wire until the gold has melted. The mixture is then cooled in cold water, and excess mercury is removed by squeezing the mixture in a chamois bag. The final product is a paste about the consistency of butter, which can be easily applied to the prepared surface.
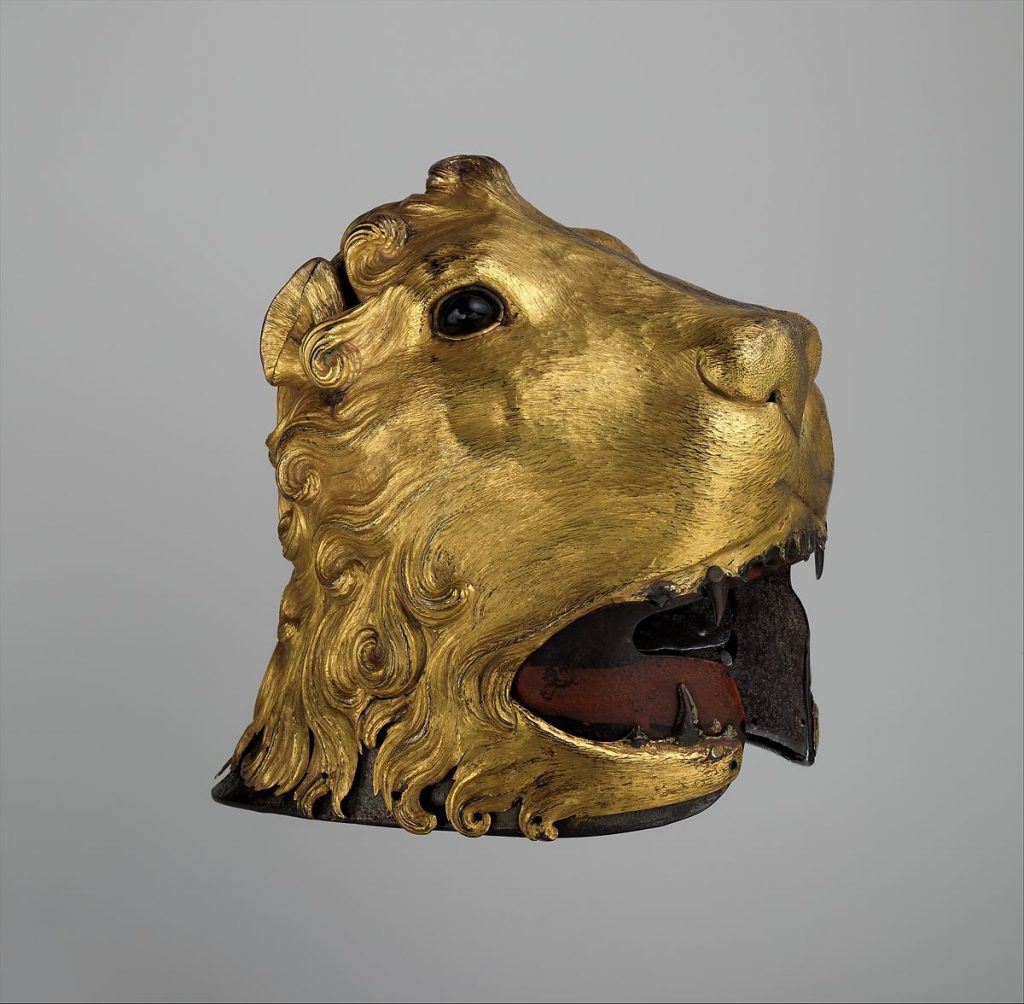
The surface to be gilded is prepared with meticulous cleaning, usually with an acid that removes not only grease and dirt but also small amounts of corrosion. Once cleaned, a silver or copper surface can be gilt, but an iron or steel surface must be further prepared by plating a thin layer of copper to the surface.
The amalgam is applied using either a brass or hog-bristle brush, or a spatula or similar tool, depending on the area to be gilt. Immediately before application, the surface is “quickened” with an application of mercury, which improves the adherence of the paste. For large areas of gilding, it was probably easier to use gold foil laid directly over mercury on the object surface, rather than the amalgam paste.
After the surface has been coated, it is necessary to remove or “drive off” the mercury. The entire piece is heated in an oven or crucible of some kind, which vaporizes the mercury. The gold left behind is now metallurgically bonded to the substrate, a bond that is more durable and long lasting than an adhesive or a mechanical bond. The gilt surface must be polished and burnished, but when complete it is bright and lustrous, a fitting decoration for masterwork arms and armor.
Further Reading
- Anheuser, Kilian. “Historic Techniques for the Gilding of Armour.” In Make All Sure: The Conservation and Restoration of Arms and Armour, edited by Robert Douglas Smith.. Leeds: Basiliscoe Press, 2006.
- Ffoulkes, Charles. The Armourer and His Craft from the XIth to the XVIth Century. London: Methuen, 1912.
- Maryon, Herbert. Metalwork and Enamelling: A Practical Treatise on Gold and Silversmiths’ Work and Their Allied Crafts. 5th rev. ed. . New York: Dover, 1971.
- Theophilus. On Divers Arts: The Foremost Medieval Treatise on Painting, Glassmaking, and Metalwork. Translated and edited by John G. Hawthorne and Cyril Stanley Smith.. New York: Dover, 1979.
- Untracht, Oppi. Metal Techniques for Craftsmen: A Basic Manual for Craftsmen on the Methods of Forming and Decorating Metals. Garden City, N.Y.: Doubleday, 1968.
Originally published by the Metropolitan Museum of Art, Heilbrunn Timeline of Art History, July 2007, under the terms of a Creative Commons 1.0 Universal Public Domain Dedication license.